Carbide Punches Manufacturers
We are carbide punches manufacturers in India. Carbide punches are tools used in industrial applications for punching holes or shaping materials such as metals, plastics, and wood. Carbide punches are made of tungsten carbide, a high-performance material that offers exceptional strength, hardness, and wears resistance.
The use of carbide punches offers several advantages over other punch materials, including improved durability, extended tool life, and reduced tool maintenance. Carbide punches are also able to maintain their sharpness and precision over a longer period, resulting in cleaner, more precise punches.
Carbide punches are commonly used in applications such as metal stamping, die casting, and wire drawing. They are available in a range of sizes and shapes to accommodate various punching needs and can be customized to meet specific application requirements.
Overall, carbide punches are a reliable and efficient tool for punching and shaping materials and are a preferred choice for many industrial applications due to their exceptional durability and performance.
Types of Carbide Punches
There are several types of carbide punches available, each designed to meet specific industrial punching needs. Here are some of the most common types of carbide punches:
- Straight punches: These are the most basic type of carbide punches, with a straight, cylindrical shape. They are commonly used for punching holes in metal, plastic, and wood.
- Step punches: Step punches have a stepped design, with a larger diameter at the top and a smaller diameter at the bottom. They are used for punching holes with a specific depth or for creating countersinks.
- Ejector punches: Ejector punches are designed to eject parts from a die after punching. They have a tapered shape that helps to remove the part from the die, and are commonly used in high-volume production applications.
- Forming punches: Forming punches are used to shape materials into a specific form or profile. They are commonly used in applications such as tube bending and wire forming.
- Knockout punches: Knockout punches are used to remove a punched part from the die after punching. They have a sharp, pointed tip that helps to push the part out of the die.
- Pilot punches: Pilot punches are used to guide the cutting action of other punches, helping to ensure accuracy and precision in the punching process.
These are just a few examples of the types of carbide punches available. Depending on the specific industrial application, there may be other types of carbide punches that are better suited to the task.
Benefits
Carbide punches offer several benefits over other types of punches, including:
- Hardness and wear resistance: Carbide punches are made from tungsten carbide, which is one of the hardest and most wear-resistant materials available. This means that carbide punches can withstand high-stress applications, resist wear and damage, and maintain their sharpness and precision over a longer period.
- Durability: Due to their hardness and wear resistance, carbide punches are highly durable and can last up to 10 times longer than traditional steel punches. This results in lower tool replacement costs and reduced downtime for tool maintenance.
- Precision and accuracy: Carbide punches can maintain their sharpness and precision over a longer period, resulting in cleaner, more accurate punches. This is important in industries where precision is critical, such as aerospace and medical device manufacturing.
- Versatility: Carbide punches are available in a range of sizes and shapes to accommodate different punching needs. They can be customized to meet specific application requirements, making them a versatile tool for a variety of industrial applications.
- Reduced tool maintenance: Due to their durability and wear resistance, carbide punches require less maintenance than other types of punches. This reduces the amount of time and resources needed for tool maintenance, resulting in higher productivity and efficiency.
Overall, carbide punches are a reliable and efficient tool for punching and shaping materials, and offer several benefits over other types of punches, including increased durability, precision, and versatility.
Application
Carbide punches are used in a wide range of industrial applications, including:
- Metal stamping: Carbide punches are commonly used in metal stamping operations, where they are used to punch holes, create shapes and forms, and cut metal sheets and plates.
- Die casting: Carbide punches are used in die casting applications to create cavities, ejector pins, and other features in the die casting mold.
- Wire drawing: Carbide punches are used in wire drawing operations to shape and form wire into specific shapes and sizes.
- Plastic molding: Carbide punches are used in plastic molding operations to create holes, threads, and other features in plastic parts.
- Electronics manufacturing: Carbide punches are used in the production of electronic components, such as circuit boards and connectors, where precision and accuracy are critical.
- Medical device manufacturing: Carbide punches are used in the production of medical devices, such as surgical instruments and implants, where precision and durability are essential.
- Aerospace and aviation: Carbide punches are used in the production of aerospace and aviation components, such as turbine blades and engine parts, where high-stress applications and extreme temperatures are common.
Overall, carbide punches are a versatile tool that can be used in a variety of industrial applications where durability, precision, and performance are critical.
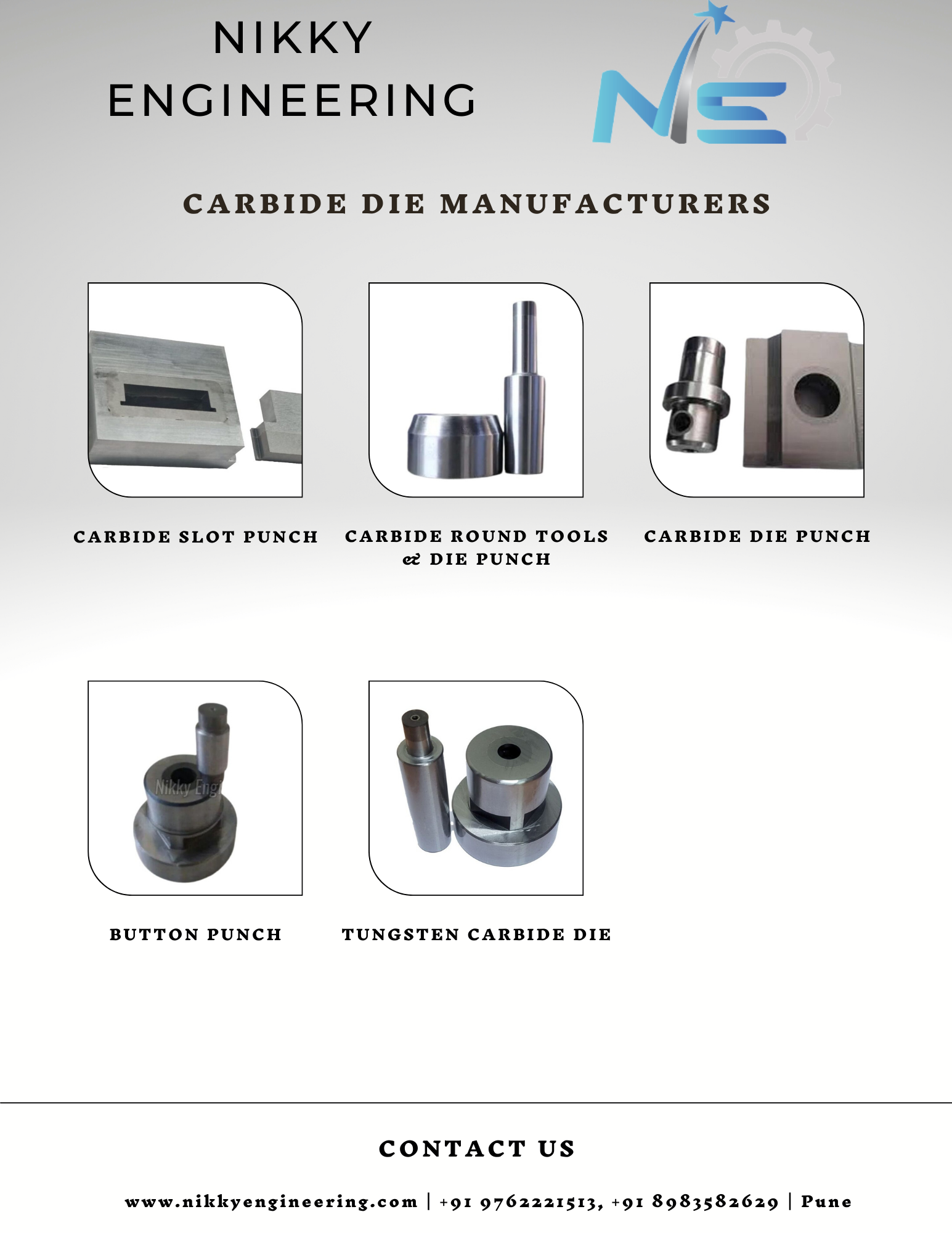